Wenn Ihr eine 3D-Metaldrucker einsetzen wollt, der eine sehr gute Qualität liefert, müsst Ihr eine große anzahl von Parameter im Auge behalten. Das ins z.B. das Material, die Energie, der Weg, die Temperatur, die Layerdicke, etc.. Dem aber noch nicht genug, auch die Geometrie hat eine massiven Einfluss auf das Ergebnis. Damit Ihr das nicht alles selber aus der Erfahrung entscheiden müsst, wird man eine Simulations-Software einsetzen. Aber auch die Ergebnisse der Simulation müssen validiert werden.
Bauplatte
Es gibt eine Reihe von Test- Artefakten, die Ihr zum justieren der Simulation drucken könnt. Aus den Abweichungen zwischen dem Soll und dem Ist ermittelt Ihr die Abweichungen. Das macht Ihr so lange, bis ihr nahe am Optimum seid. Weit weg vom Optimum ist auf dem Bild rechts der erste Balken, der hat sich bei Drucken von der Platte gelöst.
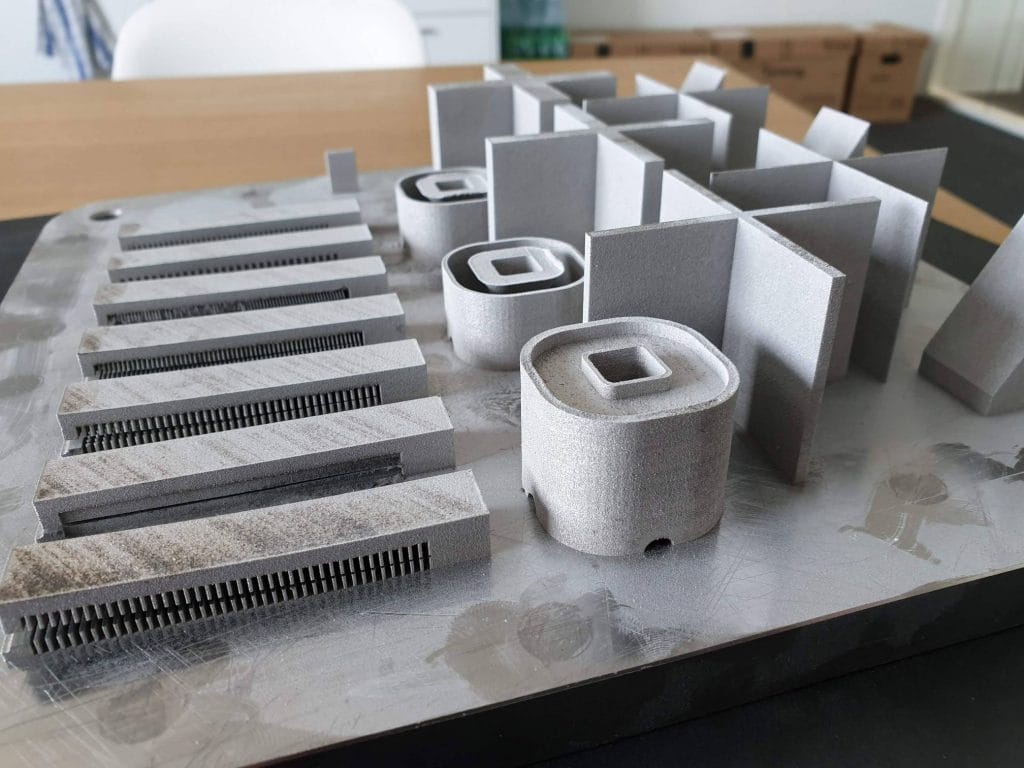
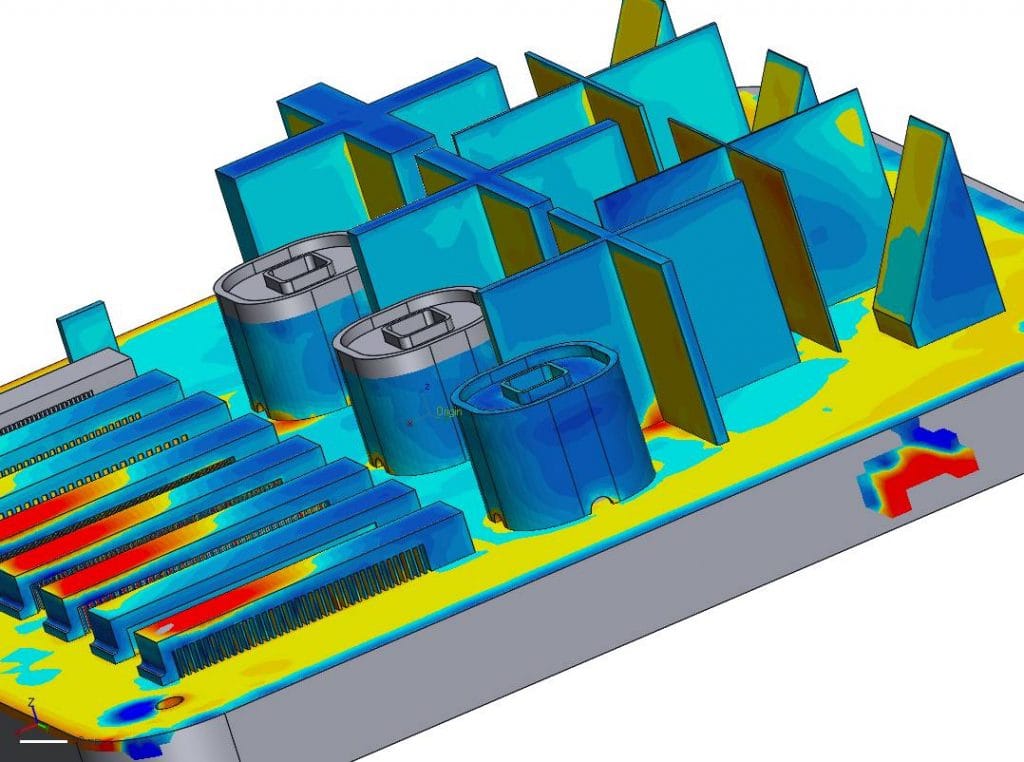
Auswertung 3D-Scan
Die Auswertung mit mit dem 3D-Scan zeigt euch anhand der Falschfarbenbilder wo Ihr große Abweichungen habt. Ich setze dazu das Control X von 3D Systems ein. Zugeben, neben dem 3D-Scannen können diese Abweichungen auch mit einer taktilen Messmaschine bestimmt werden. Meiner Erfahrung nach hat das 3D-Scannen eine Reihe von Vorteilen.
- Der Falschfarbenplot zeigt euch die Stellen, an denen Ihr die größten Abweichungen habt.
- Nach dem Ihr das Teil mit dem Scanner erfasst habt könnt Ihr beliebig die Ausrichtung verändern, um ein Feature auszuwerten und dabei nur die Formabweichung bewerten. Den Lagefehler kompensiert Ihr dabei durch die neue Ausrichtung.
- Entdeckt Ihr bereicht die Ihr weiter untersuchen wollt könnt Ihr das auf Basis der vorhandenen Scandaten erledigen ohne das Teil nochmal an die Messmaschine zu bringen.
- Die 3D-Scandaten könnt ihr Platzsparend auf der Festplatte archivieren.
- Die 3D-Scandaten könnt einfach verschicken und euch einen Rat vom Hersteller oder einem Partner einholen.
- Druckt Ihr das selbe Teil zweimal, könnt Ihr auch eine Auswertung zwischen den beiden IST Daten vornehmen
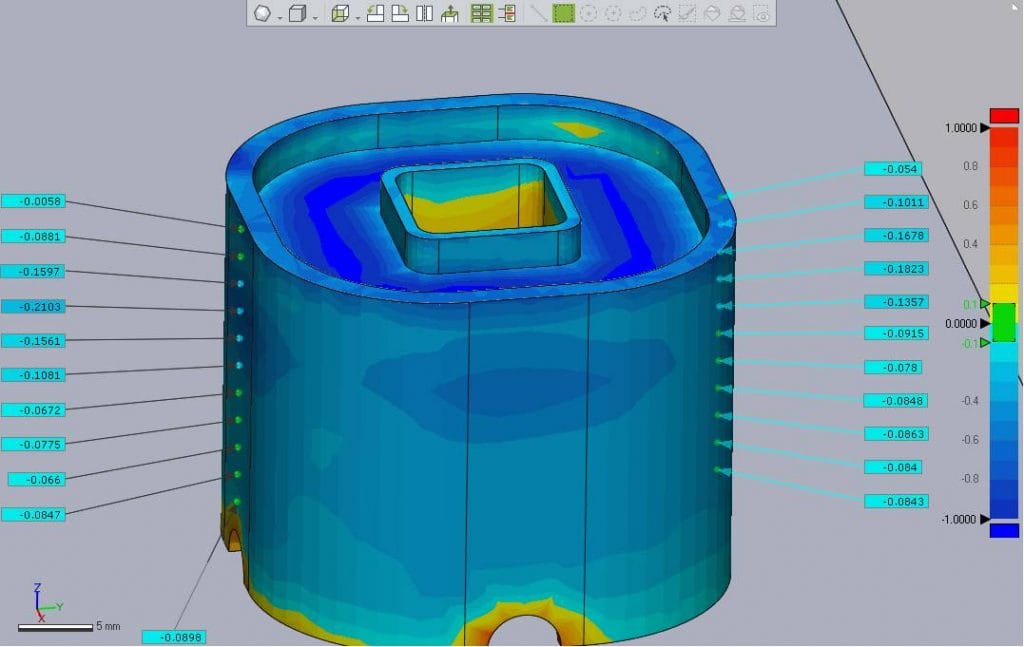
Neben den Auswertungen, für die Optimierung des Druckprozesses könnt Ihr den 3D-Scanner natürlich auf für die Qualitätssicherung von Bauteilen, die im Auftrag drucken sollt einsetzen. … und nicht zu vergessen könnt Ihr den Scanner für das Reverse Engineering einsetzen.