Bei den 3D-Scanner von Creaform gibt es zwei Parameter, die sich nicht auf den ersten Blick erschließen. Die Hilfe liefert dazu auch wenig erhellendes. Es geht um die Randgenauigkeit und das Dezimieren. Beide Parameter haben eine Einfluss auf die Qualität und die Rechenzeit bei der Erstellung des Netztes. Um der Sache auf den Grund zu gehen habe ich eine Borschablone und ein Gehäuse mit dem HandyScan Black | Elite erfasst.
Optimieren durch Dezimieren
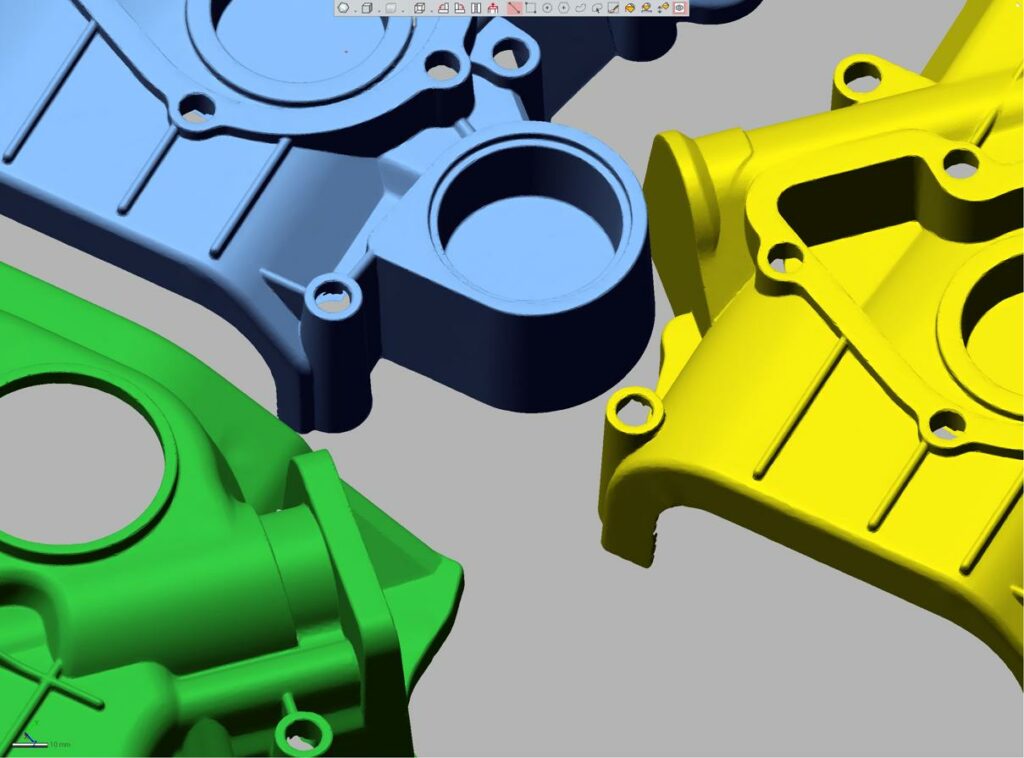
Beim automatischen Dezimieren werden Bereiche mit wenig Details und Krümmung gröber vernetzt als flache Bereichen. Zur Veranschaulichung eine Schreibtischplatte kann ich mit zwei Dreiecken perfekt abbilden. Der positive Effekt vom Dezimieren ist das die Anzahl der Dreiecke drastisch reduziert wird. Ohne großen Qualitätsverlust kann man so ca. 60% der Daten einsparen. Der Nachteil ist, dass es Rechenzeit kostet das Model zu Dezimieren. Bei kleinen Modellen wirkt sich das nicht sehr stark aus bei dem Beispiel hat die Berechnung mit Dezimieren 20 Sekunden gedauert ohne das Dezimieren war die Berechnung in 18 Sekunden fertig. Bei großen Modellen sind die Unterschiede gravierender.
Neben dem VXElements kann man die Modelle auch im Design X reduzieren. Das Design X bietet dabei noch weiter Parameter an, um auf das Ergebnis Einfluß zu nehmen.
In dem Bild seht Ihr dreimal den selben Scan.
- Blau ohne dezimieren
- Gelb mit Deszimieren im VXElements
- Grün mit Dezimieren im Design X
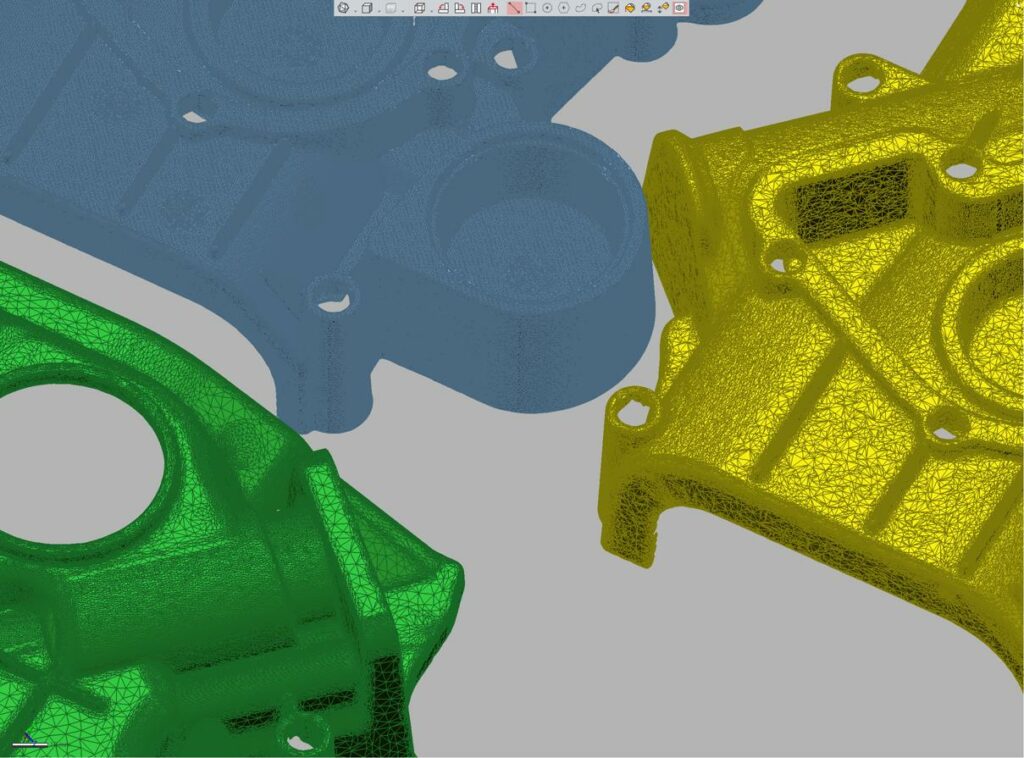
Was man gut erkennen kann, ist das Bereiche mit starker Krümmung mit kleinen Dreiecken Vernetzt werden und Flache Bereiche mit großen Dreiecken vernetzt werden. Wenn man das Resultat vom Design X mit dem VXElements vergleicht, fällt auf dass die Dreiecke im Design X (grün) stärker an den Übergängen ausgerichtet sind. Das hat beim Reverse Engineering bei der Selektion Vorteile. Das ist aber eher marginal.