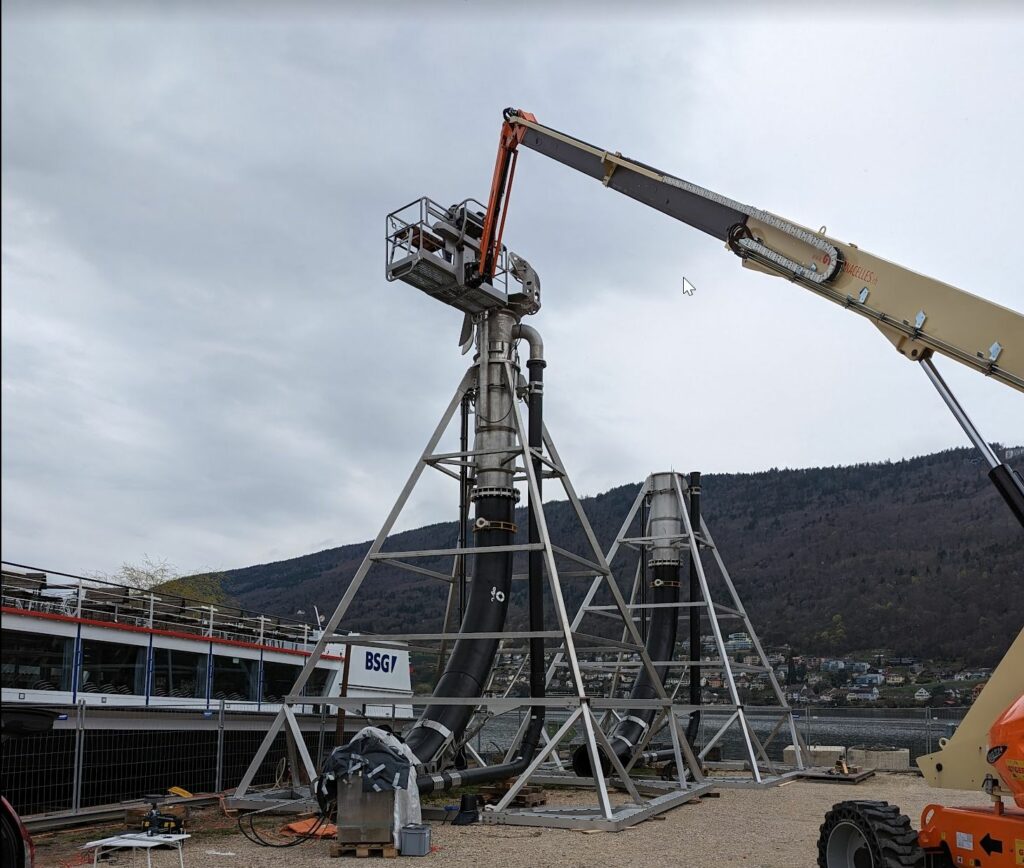
Vor kurzem erhielten wir einen Auftrag vom Konstruktionsbüro Hersche zur Vermessung einer Rohrleitung. Dabei handelt es sich um einen Ansaugstutzen für die Trinkwasserversorgung. Diese Stutzen wird auf ca. 40 Meter Tiefe im Bielersee verankert. Eine eingeschleppte Muschel aus dem Schwarzen Meer ist für einen starken Muschelbewuchs verantwortlich. Um den Stutzen von dem Muschelbefall zu befreien, wird dieser von einer Maschine gereinigt. Für den sicheren Betrieb dieser Maschinen ist es notwendig, dass das Rohr eng toleriert wird.
Das Vermessen eines Rohrs klingt einfach, oder? Der Einstieg befindet sich jedoch auf einer Höhe von 10 Metern, das Rohr hat einen Durchmesser von 700 Millimetern und es sollte ein etwa 9 Meter langes Stück vermessen werden.
Aus diesem Setup ergeben sich mehrere Herausforderungen:
- Es wird ein handgeführter Scanner benötigt, der auf einer großen Distanz ein sehr genaues Tracking garantiert
- Das Anbringen der Targets und das Vermessen der Leitung kann nur hängend in einem Klettergurt durchgeführt werden
- Das Rohr musste vor dem Vermessen gereinigt werden, da es teilweise mit Sediment behaftet war. Das zweite Rohr musste gereinigt werden, da es aus der Produktion noch mit einem Gleitmittel versehen war.
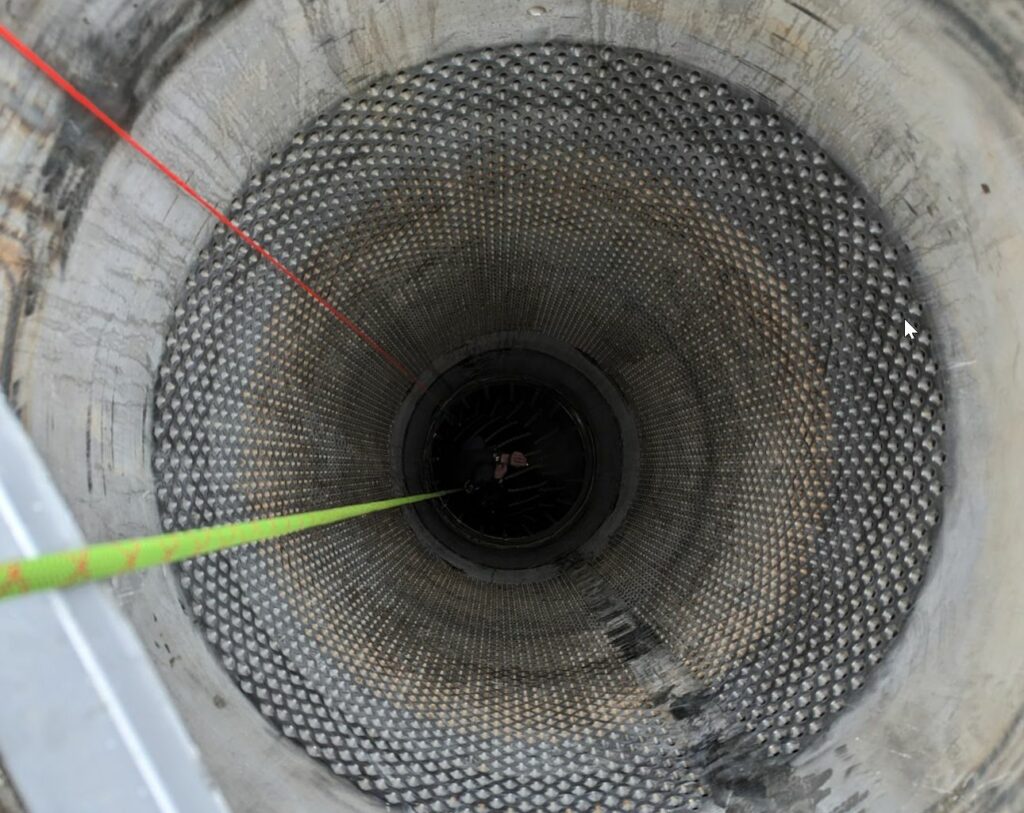
Die Vermessung haben wir mit unserem HandySCAN Black | Elite durchgeführt. Für die Messung wurden im Rohr 2000 Targets angebracht und später wieder entfernt. Insgesamt benötigten wir dafür 8 Stunden, jedoch war die eigentliche Vermessung bereits nach etwa einer Stunde abgeschlossen.
Es ist offensichtlich, dass es durch die Produktion und die Montage nicht realistisch ist, ein Bauteil zu erhalten, das man direkt mit den CAD-Daten vergleichen kann. Daher haben wir das Rohr auf Basis der gemessenen Daten per Reverse-Engineering als „as-built“ nachgebaut und dieses Modell für die Analyse der Abweichungen genutzt.
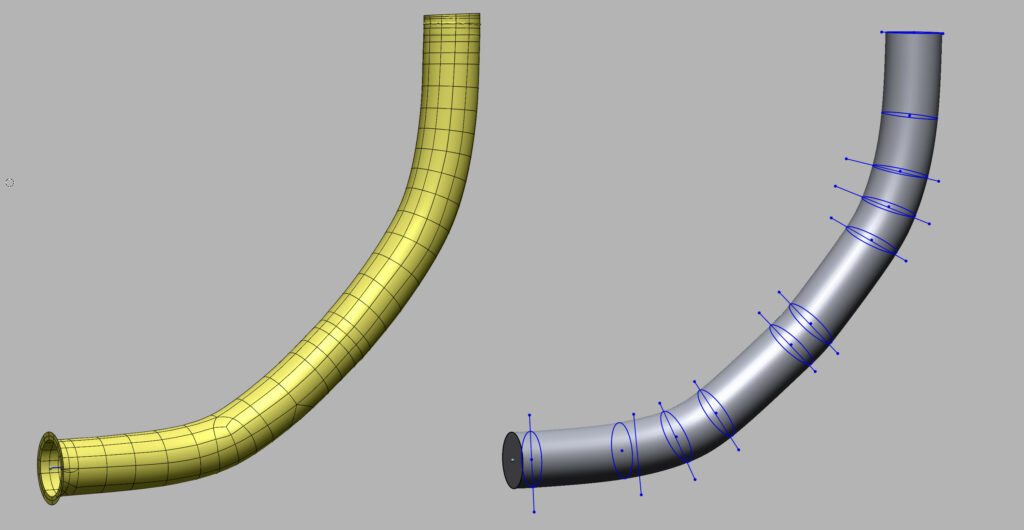
Für die Vermessung haben wir das Control X eingesetzt, ein leistungsfähiges Inspektions- und Analysetool, das in der Lage ist, komplexe Geometrien und Oberflächen zu analysieren. Durch die Verwendung von Flächenfalschfarben-Plots konnten wir die kritischen Stellen innerhalb der Rohrleitung schnell und effizient identifizieren. Diese farbigen Darstellungen ermöglichen es, Abweichungen und Unregelmäßigkeiten auf einen Blick zu erkennen, indem verschiedene Farben die unterschiedlichen Abweichungen von der Soll-Geometrie repräsentieren.
Nachdem wir die kritischen Stellen identifiziert hatten, führten wir eine 2D-Konturabweichungsanalyse durch, um die Abweichungen quantitativ zu bestimmen. Dieser Schritt half uns dabei, die genauen Bereiche der Abweichungen und deren Ausmaß besser zu verstehen. Durch die Kombination dieser beiden Methoden konnten wir eine umfassende Analyse der Rohrleitung durchführen und sicherstellen, dass sie innerhalb der erforderlichen Toleranzen liegt.
Die gesammelten Daten wurden in einem Bericht an den Kunden übergeben, der gezielte Empfehlungen für notwendige Korrekturmaßnahmen enthielt, basierend auf unserer umfassenden Analyse der Vermessungsergebnisse.
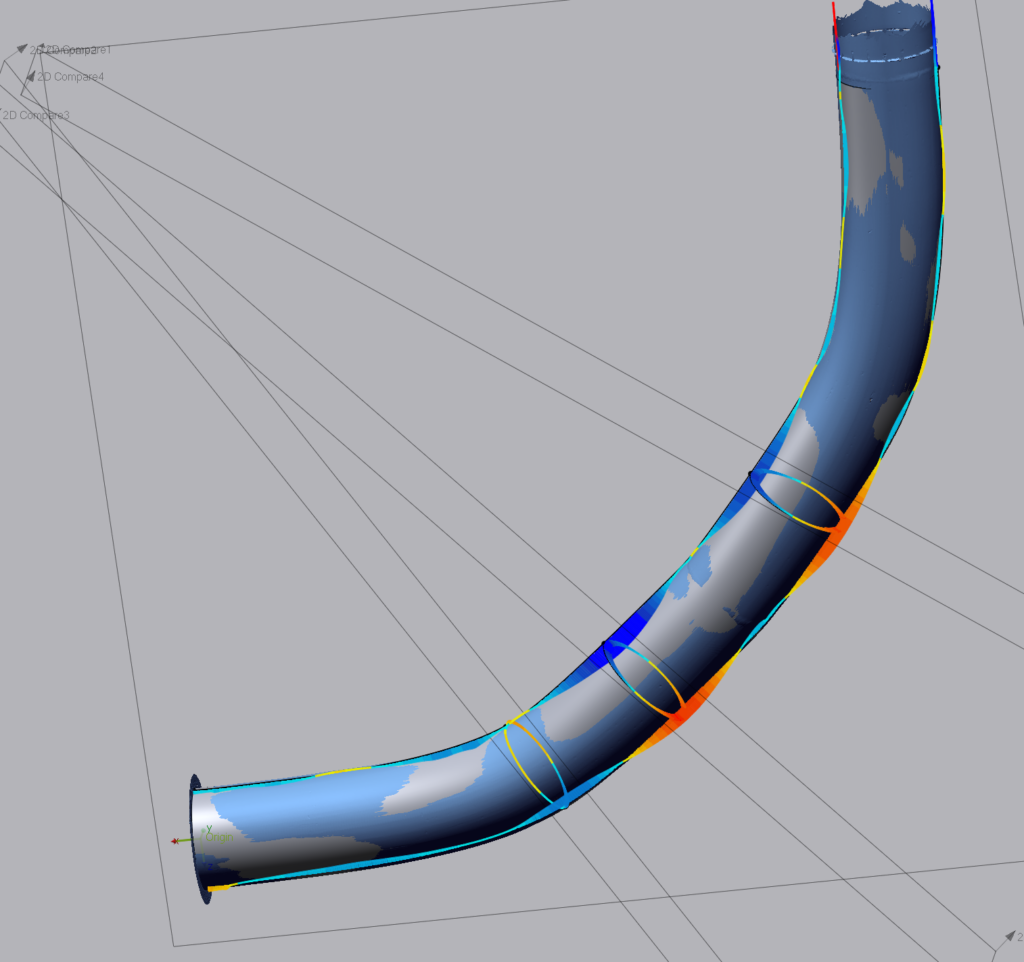
Wenn Sie ebenfalls an einem kleinen Vermessungsabenteuer interessiert sind, dürfen Sie sich gerne bei uns melden. Unser Team verfügt über die nötige Erfahrung und das Know-how, um auch in schwierigen Situationen präzise Vermessungen durchzuführen. Wir freuen uns darauf, Ihnen bei der Lösung Ihrer Vermessungsherausforderungen zu helfen und gemeinsam die beste Lösung für Ihr Projekt zu finden.